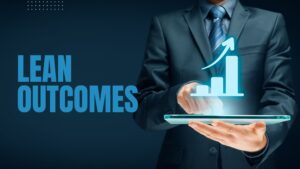
In a blog post my colleague Travis Ratnam wrote on the essence of lean transformation, he explored the benefits of this transformational approach to business excellence. But we know through our years of experience at Adonis Partners that the outcomes of a lean transformation can vary depending on the specific context, industry, and goals of the organization. With that said, here are some typical outcomes that individuals, teams, and businesses can expect as you take on this journey:
Individual Level
Increased Skills and Knowledge:
Empowerment:
Improved Morale:
Team Level
Collaboration:
Efficiency Gains:
Quality Improvement:
Cross-Functional Cooperation:
Business Level
Cost Reduction:
Improved Customer Satisfaction:
Faster Time-to-Market:
Increased Flexibility:
Strategic Alignment:
Cultural Transformation:
Supply Chain Optimization:
It’s important to note that the outcomes of a lean transformation may take time to materialize, and the level of success depends on the commitment of leadership, the engagement of employees, and the specific challenges and opportunities within the organization. Continuous Improvement is a key aspect of lean thinking, so organizations should see this as a long-term journey for sustainable, lasting success and excellence.
Barry is an “Operator” who was given the opportunity to learn and practice Lean Six Sigma after 20 years of leading large organizations in North America and Asia in the Technology sector. He earned Master Black Belt status and was recruited back into executive operations roles to lead and develop a culture of Continuous Improvement.