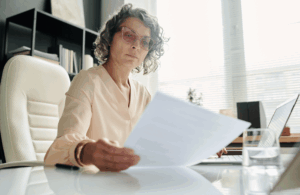
Root Cause Analysis (RCA) is a process used to identify a problem or unexpected occurrence, such as a product not being received as expected. There are multiple ways to conduct a root cause analysis, but the ultimate aim is to improve the quality of the process or products and take systematic measures to become more effective in the future. In this article, we will discuss a few different root cause analysis strategies that will help your organization identify underlying problems.
Ask the 5 Whys
While a simple concept in theory, the 5 Whys Analysis aims to discover the initial reason why a problem occurred. The goal of the 5 Whys is to ask why, and then understand the why behind the why so the root cause can be determined. The answers to the whys should be fact-based and succinct.
Use a Fishbone Diagram
The fishbone or cause-and-effect diagram is used by grouping causes into categories, such as people, materials, methods, etc. While the categories may vary depending on the industry you are in, the fishbone diagram aims to create a visual for your team to categorize causes and sub-causes behind an issue.
Failure Mode and Effect Analysis (FMEA)
FMEA is a tool used primarily in risk analysis to identify areas where a solution could fail. The goal of FMEA is to analyze how failure occurs in a system and then determine ways to prevent failure from occurring again. FMEA is a tool that can be used before problems occur as a way to prevent problems from occurring in the future.
There are several strategies and techniques that have been developed to conduct a root cause analysis. Here at Adonis Partners we provide Kaizen Event Facilitation and Lean/Six Sigma Project Execution that will help your organization tackle tough challenges and identify as well as prioritize the true root causes behind issues.
Cate has 20+ years of experience in the corporate world and has held positions in finance, supply chain, account management, product management and project management. While she has experience in logistics, manufacturing and healthcare, her main area of expertise lies in big data and the service industry.