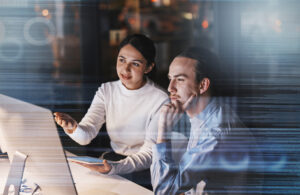
In a blog post my colleague Travis Ratnam wrote on the essence of lean transformation, he explored the benefits of this transformational management philosophy for achieving business excellence. Implementing lean practices can indeed deliver immediate and quantifiable outcomes, providing several benefits to a business.
Here’s how:
Waste Reduction:
Improved Process Efficiency:
Increased Productivity:
Enhanced Quality:
Inventory Reduction:
Customer Satisfaction:
Cultural Change and Employee Engagement:
Cost Savings:
Adaptability to Change:
Data-Driven Decision Making:
In summary, a lean transformation can deliver immediate and quantifiable outcomes by addressing inefficiencies and waste in processes. The benefits extend beyond cost savings to include improved quality, customer satisfaction, employee engagement, and overall organizational agility.
At Adonis Partners, we have real-world, long-term experience across varying industries to help guide leaders in their journey to implement a lean transformation and culture.