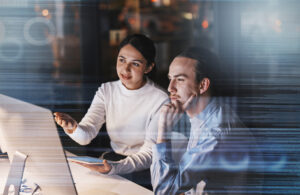
The elimination of waste is a core principle behind a lean-driven organization’s efforts toward process excellence. Waste goes beyond tangible and visual defects at the end of the line – even when the “line” is one out of a transactional process; for example, errors in a form that cannot render a claim in an insurance company. In fact, the worst types of waste are the ones that, if left unchecked, build up over time and no one can properly investigate. These are the eight types of waste any process can carry at any point in time. Understanding what they are is an important first task in eliminating or at least minimizing their impact in the process.
Transportation: All unnecessary transportation of people and/or material that adds time to the process but not value (filing, stocking, stacking, moving parts between departments).
Inventory: Found excessively in work-in-progress (WIP) or finished goods. It is usually caused by large lot production or processes with long cycle times. This is normally identified in batch and queue systems.
Motion: Any motion of people and/or machinery that do not add any value to the customer. Excessive motion might increase process time and opportunities for errors (walking, reaching, bending).
Waiting and delays: Idle time that arises when dependent or downstream activities are not fully synchronized. Waiting promotes workflow stoppage (people waiting for processes to finish or information to arrive at their workstation, incomplete forms or applications, delays in reviews and approvals, delayed testing).
Over-processing: Extra operations and enhancements that are invisible and do not add any value to the customer (excessive sign offs and approvals, detailed documentation, extraneous planning activities).
Over-producing: Producing too much or too early or before it is needed. This is often a result from producing to speculative demand (preparing extra reports that are not read or acted upon, working to get ahead, “push” production – produce it, inventory it, and hope that someone will buy it).
Defects and rework: Products and/or services that do not conform to specifications or to customers’ expectations causing customer dissatisfaction. Correcting errors, redoing work (incorrect or incomplete data entry, visible defects in products, wrong information), and creating nothing of value to anyone.
Under-utilized skills: Any failure to fully utilize the time and talents of people. This particular waste might create low employee morale, loss of creativity and initiative, loss of employees and/or high turnover.
How Adonis Can Help
Properly identifying and eliminating waste are key components of the Lean journey. Here at Adonis, we provide training and ongoing support that will help your organization reduce, if not completely eliminate, sources of waste in your process that might be hindering the maturity of your continuous improvement efforts.