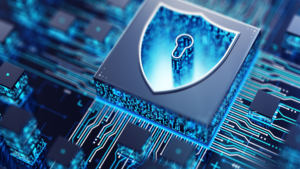
What is TPM?
TPM, or Total Productive Maintenance, is a maintenance program that combines equipment maintenance with the manufacturing process. TPM was originally created by Seiichi Nakajima in Japan and was first implemented in 1971 by Nippondenso, a Toyota parts manufacturer. It has since been adopted and adapted by various organizations.
Since production relies so heavily on machines and equipment to get jobs done, the losses that can occur from any of the machines or equipment malfunctioning leads to a loss in productivity and money. TPM aims to minimize losses, increase production, and create higher job satisfaction by adopting a unique system which involves production operators in the maintenance process.
There are 6 main losses that TPM focuses on reducing:
TPM aims to eliminate these losses by implementing the 8 pillars of TPM, which are:
Why should you care?
TPM can reduce manufacturing costs by 30% and can also increase Overall Plant Efficiency (OPE). Aside from manufacturing costs and efficiency, it also saves time lost by trying to get a broken or idling machine moving. Most importantly, it helps the business run more smoothly, while also boosting morale and increasing safety for employees. Reducing the frustration placed on workers creates a better work environment and increases productivity. The focus on efficiency, equipment maintenance, and the employee satisfaction is what makes TPM a viable maintenance program to use in the production process.
Be passionate about continuous improvement – I am a believer in the importance of capability building to enable individuals and organizations to achieve sustainable benefits through continuous improvement.