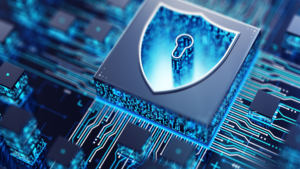
FMEA, short for Failure Mode and Effects Analysis is a forward-thinking and powerful risk mitigation tool that Continuous Improvement practitioners use. It is a living document, used to anticipate and prevent failure from occurring. Originated in the U.S. military in the 1940s, it was first expanded to the aerospace, nuclear, food, and automotive industries. Nowadays, virtually every industry uses the FMEA concept to some extent.
How does it work?
An FMEA can help mitigate undesired outcomes in a process when things can potentially go wrong – and often things do go wrong. It works by documenting and building an analysis that:
1. Recognize potential failure: what can go wrong with this step of the process?
2. Evaluate potential failure: what type of failure could the process experience?
3. Weigh importance of potential failure: how much should we prioritize action to mitigate.
4. Identify actions to minimize risk: what can be done to mitigate the undesirable outcomes?
Building an FMEA is a Team-based exercise! These four steps should be taken into account whenever a Team is developing a Process FMEA:
1. Select the process
2. Assemble the Team
3. Map the process
4. Brainstorm Failure Mode and Effects (build the FMEA)
RPN (Risk Priority Number)
To weight the contribution of each step of the process, along with their respective impact on the potential undesired outcomes, the FMEA uses a Risk Priority Number criteria that basically investigates three parameters:
1. Occurrence: the frequency of which the failure will likely happen
2. Severity: how bad this is going to be if the failure does happen
3. Detectability: how detectable is the failure if it does happen
Developing and deploying FMEA requires some experience with the approach. We encourage you to leverage an FMEA and help your organization apply this concept to improve process reliability and quality.
Passionate result seeker. Building a strong foundation gains the agility to sustain moments of intense pressure. The first step is to act.