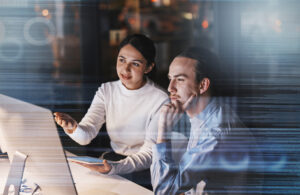
The essence of Lean transformation lies in optimizing processes for sustainable growth and creating a culture of continuous improvement within an organization. Originating from manufacturing principles pioneered by Toyota, Lean thinking has been widely adopted across various industries. The fundamental goal of Lean transformation is to eliminate waste, enhance efficiency, and deliver greater value to customers.
At Adonis Partners we operate by Lean principles and believe that businesses that adopt these principles will have a more engaged and positive corporate culture in addition to the value Lean principles bring to operational end goals.
Here are nine key principles of Lean transformation and how they foster operational excellence:
Lean transformation is not a one-time event but a dynamic and ongoing journey. It requires commitment from leadership, engagement from employees, and a willingness to adapt and evolve. By embracing Lean principles, organizations can become more agile, responsive, and capable of delivering higher value to customers while operating more efficiently.