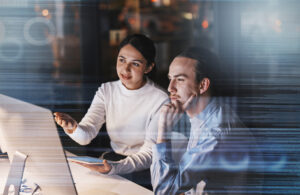
In multi-site operations, achieving strategic alignment across teams is a critical challenge. Misalignment leads to inefficiencies, duplication of efforts, and disengaged employees who struggle to see how their work contributes to the company’s success. To drive sustainable growth and value creation, leadership teams must ensure all functions are working toward common objectives.
Continuous Improvement (CI) methodologies such as Lean Six Sigma (LSS) and DMAIC (Define, Measure, Analyze, Improve, Control) provide structured frameworks to ensure company-wide alignment. These methodologies facilitate problem-solving, encourage data-driven decision-making, and promote cross-functional collaboration.
By integrating these frameworks, organizations can create a culture of collaboration and accountability, improving execution speed and value creation.
Case Study: A healthcare company struggling with operational inefficiencies due to unintegrated acquisitions implemented Lean and Project Management training. The result? Standardized processes, repurposing of 20 employees, and an annual savings of $200K. Read the full case study.