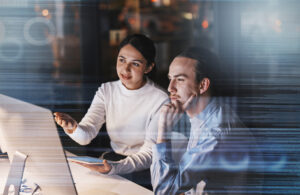
What is Error Proofing?
Also known as Poka-Yoke, from poka (inadvertent errors) and yokeru (to avoid), error proofing is the technique continuous improvement practitioners use to prevent errors that ultimately lead to defects in a process. Poka-Yoke is commonly used in manufacturing however it is highly applicable to transactional processes as well.
How To Use Poka-Yoke
There are basically five approaches to error proofing a process: elimination, replacement, facilitation, mitigation, and flagging. For example, a college admissions department uses these approaches, along with technology, to reduce the number of wrong applications in any given program.
1. Elimination: by using a postal code database system, the department ensures that no application is submitted with a wrong postal code. A simple and common practice that completely eliminates the chance of error.
2. Replacement: this approach has to do with automation that can be used to prevent human errors. For example, this admissions department has an automated system of notifications that ensures that applications are moving through the process as steps are being completed by the applicant.
3. Facilitation: related to work instructions that aim at minimizing chances of error, the department maintains updated documents online and with ease of access. These work instructions serve admission committees with clear guidelines about the application approval process. For example, how to conduct a final interview with the applicant.
4. Mitigation: it aims at lessening the impact of errors anywhere during the process. If an application for a program somehow ends up in a different program, there is a protocol in place to remediate the error and get the application on the right track again.
5. Flagging: the least desirable approach is to simply inspect and indicate where the error has occurred, ideally before it reaches the final consumer of the product or service. For example, a wrongful charge to an applicant due to an error in the system.
Notice how these five approaches move progressively from least costly to most costly. Preventing a defect by completely eliminating the source of error (elimination) helps a system to avoid an entire chain of reaction, which can be costly. Inspecting at the end of the process (flagging) can be very costly and could also potentially affect the reputation of the organization if the defect reaches the customer.
How Adonis Can Help
Poka-Yoke is a key tool in implementing improvements in a process. Here at Adonis, we provide training and ongoing support that will help your organization to achieve lower rates of defects and become a process excellence driven benchmark in the industry.
Great leaders share, teach, coach, support, and appreciate their people. Regardless of what is on their plate, they invest the time to know them personally, and what motivates them. I am always challenging myself and others to improve. Connecting with people to help them solve complex issues, push past obstacles and create repeatable processes is what I enjoy most.